An ambitious program developed at the MUHC delivers impressive results
Material incident-accident management system praised by Health Canada
Every day healthcare workers use hundreds of different medical products and devices, from simple examination gloves, bandages and syringes to infusion pumps, defibrillators and surgical lasers. When defective or improperly used, these products cause incidents or accidents that may put patients at risk. Reporting those events is therefore critical.
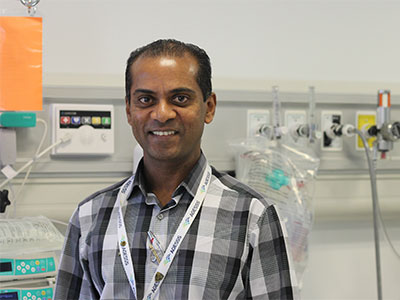
Last summer, the McGill University Health Centre (MUHC) adopted a standardized system that allows a task force to quickly evaluate risks associated with medical products in order to decide whether or not to proceed with a voluntary withdrawal. Since its implementation, the Material Incident Accident Management (MIAM) system has drastically reduced the turnaround time for a decision from 181 days to only seven days.
“As soon as the program went live, it dropped to 38 days and it kept going down. Our target is 48 hours, and we’re getting there,” says Philippe Bexton, MUHC Patient Safety officer and coordinator of the MIAM project, which brought together participants from Material Management, Procurement, Quality, Nursing and Transition Planning starting in October 2014, as the MUHC was purchasing new equipment and materials in preparation for the move to the Glen site. At that time, a critical product-related event and several smaller cases revealed the shortcomings of the management process in place.
“We found that the procedure wasn’t standardized,” he says. “In some cases, clinicians were contacting the manufacturer directly; in others, they were contacting different MUHC services: Procurement, Quality, Patient Safety, etc. We would also have to wait an average of three months for the manufacturer’s evaluation after reporting an event. Now we don’t wait anymore. We rapidly evaluate the risk internally – using an algorithm designed during a Lean Six Sigma Kaizen event – and act based on the results, in order to minimize the risk for our patients.”
47777 is the number to call
In order to accelerate the process, a new customer service phone number was created – 47777 – making it easier for medical staff to report issues.
“For example, when a line is punctured or a catheter isn’t working, all they have to do is dial 47777. A customer service representative will guide them on what to include on the Incident-Accident Report and instruct them to keep the product for pick-up,” says Procurement Manager Angie Presta, who has been presenting MIAM to various teams throughout the MUHC. “It’s important to do it as fast as possible because we want to evaluate the risk quickly to prevent other incidents elsewhere.”
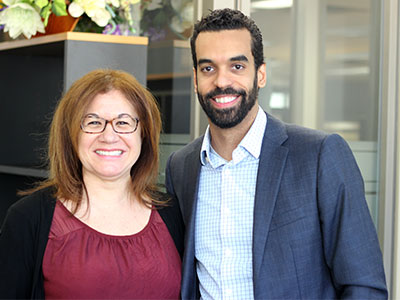
Nurse Manager Siva Moonsami has used MIAM a few times and is pleased with the results.
“We had a problem with an expensive piece of equipment that kept leaking,” says Siva, who supervises 50 nurses in the Intensive Care Unit (ICU) at the Montreal Neurological Hospital (MNH-MUHC). “I called 47777, followed the steps, and in less than 24 hours an officer came to pick it up. The next day, I got a follow-up call with information from the manufacturer. The system works.”
All information gathered during that first phone call is entered into the newly developed MIAM database. A partnership with Health Canada makes it possible to add indicators from outside the MUHC to the file.
“We are one of 14 institutions participating in the Canadian Medical Device Sentinel Network (CMDSNet), a Health Canada program created to improve the safe use of medical devices,” Philippe explains. “When we file a report, an automated email is sent to CMDSNet, which performs an environmental scan of similar events in Canada, the US, England, Switzerland and Australia.”
After the results of that scan are entered into the database, the system comes up with one of two decisions: either no action is required or a task force is summoned to determine if the product should be withdrawn. Managers of the unit where the event occurred receive an automated email informing them of the outcome of the process.
“Follow-up is very important. We want to empower managers so that they become an active part of this procedure and communicate it to their team,” says Angie.
The strategy seems to be working. Siva, who already encouraged nurses to file incident reports, made sure to explain the new procedure to his team.
“If something happens on the weekend or at night, they know what to do,” he notes. “It takes discipline, but the bottom line is patient and employee safety.”
Recognition from Health Canada
In 2015, the MUHC received a Certificate of Appreciation for Dedication to Patient Safety from Health Canada for the MIAM system.
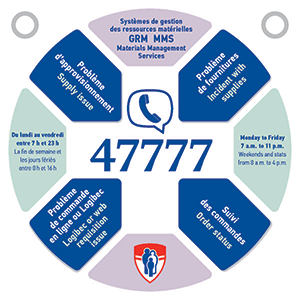
The project sponsor, Associate Director of Procurement and Material Management Paul Harmat, attributes the success of the MIAM project to the dedication of the team.
“Using basic lean principals, the different departments decided that patient safety and supply quality were a priority and they invested their time accordingly,” he says. “Not only did they recognize that there was an opportunity to make the situation better, they did something about it. I am very proud of the team and what they accomplished.”
Despite the success, the MIAM team will not rest on its laurels.
“MIAM is part of a continuous improvement process,” says Philippe. “We’ll keep on looking at ways to give better service to front-line users and minimize risks for patients.”
Did you know?
A survey conducted among 2,341 employees during the Glen orientation sessions found that 55 per cent of respondents did not know they should be reporting material-associated incidents and accidents.