Reprocessing of medical devices : Not widely known, but essential!
At the MUHC, more than 100 attendants work in the Medical Device Reprocessing Unit, commonly known as the MDRU. They work 24 hours a day, 7 days a week.
A unidirectional process
A double-door equipment barrier separates the areas of this department. What enters contaminated comes out decontaminated and/or sterilized. The areas are sealed, with access provided through separate entrances to eliminate the risk of cross-contamination. We are in the Medical Device Reprocessing Unit (MDRU), essentially the heart of the hospital, because without it, medical staff would not have sterile instruments for their procedures and interventions.
A rigorous operating cycle
After a clinical procedure or surgical operation, all used material is pre-cleaned at the point of use before being placed in a transport cart. The destination is the “soiled” transport elevator, which carries the various instruments and their biological, bacterial, or viral contaminants. This elevator leads to the MDRU’s decontamination room. It is here that surgical instruments undergo multiple treatments, starting with a wash using an enzymatic solution in large-capacity washers and decontaminators.
"It is sometimes necessary, with more delicate surgical instruments, to perform a manual wash. We also use ultrasounds to dislodge stubborn residues," says Micael Lampron. He is well acquainted with the ins and outs of the MDRU, having spent 23 years there as an attendant before becoming a manager.
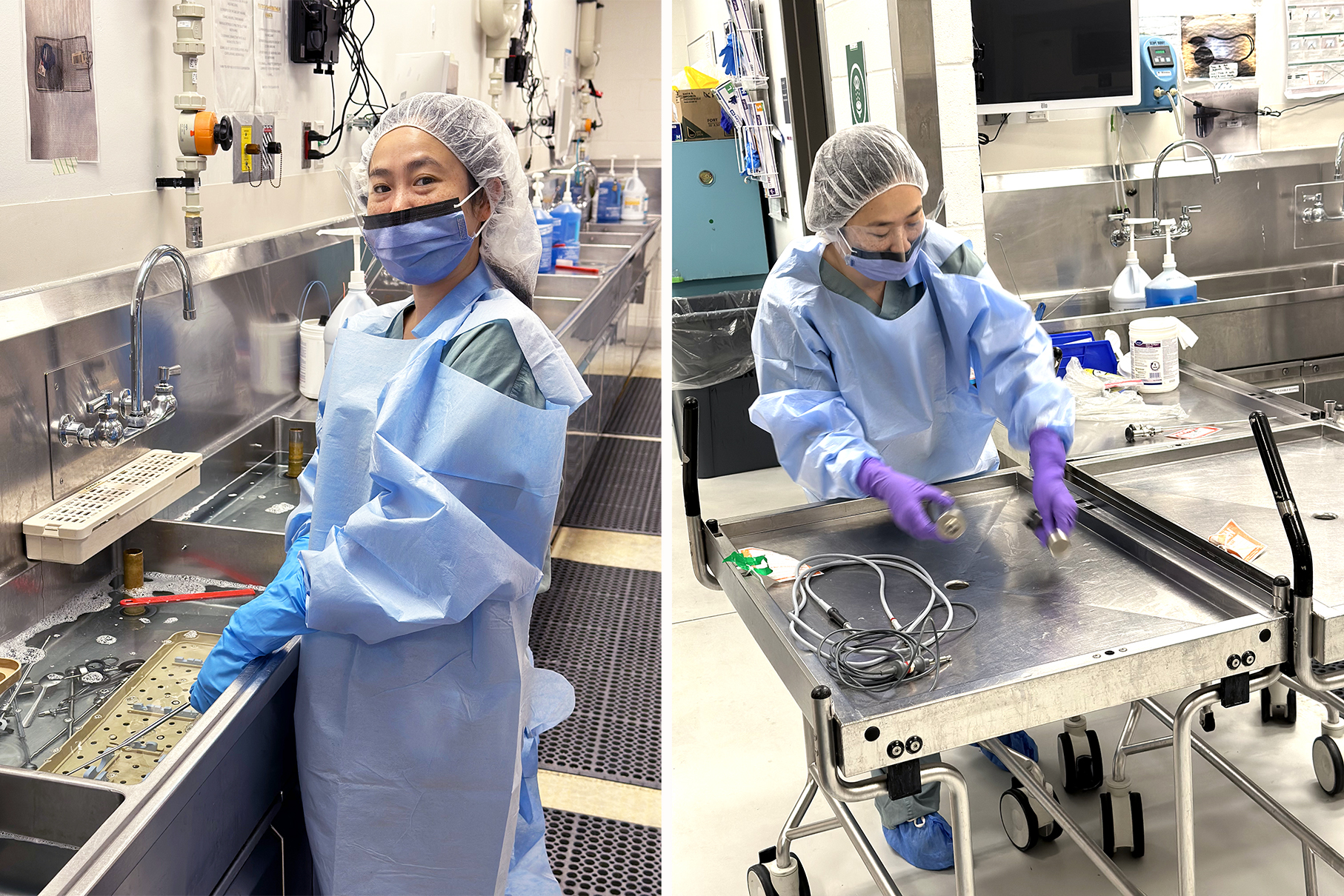
"The equipment is then ready to move to the clean side, where it is inspected, reassembled, and packaged," explains Diane Raymond, who is giving us a tour along with Enza Volpe, who has just joined the department as a manager. Reassembling is a complex operation, and each tray of tools has its own barcode and instruction manual—or recipe—stored in the database. The instruments for the da Vinci robot, which allows for minimally invasive surgery and is controlled remotely by a computer, are treated separately.
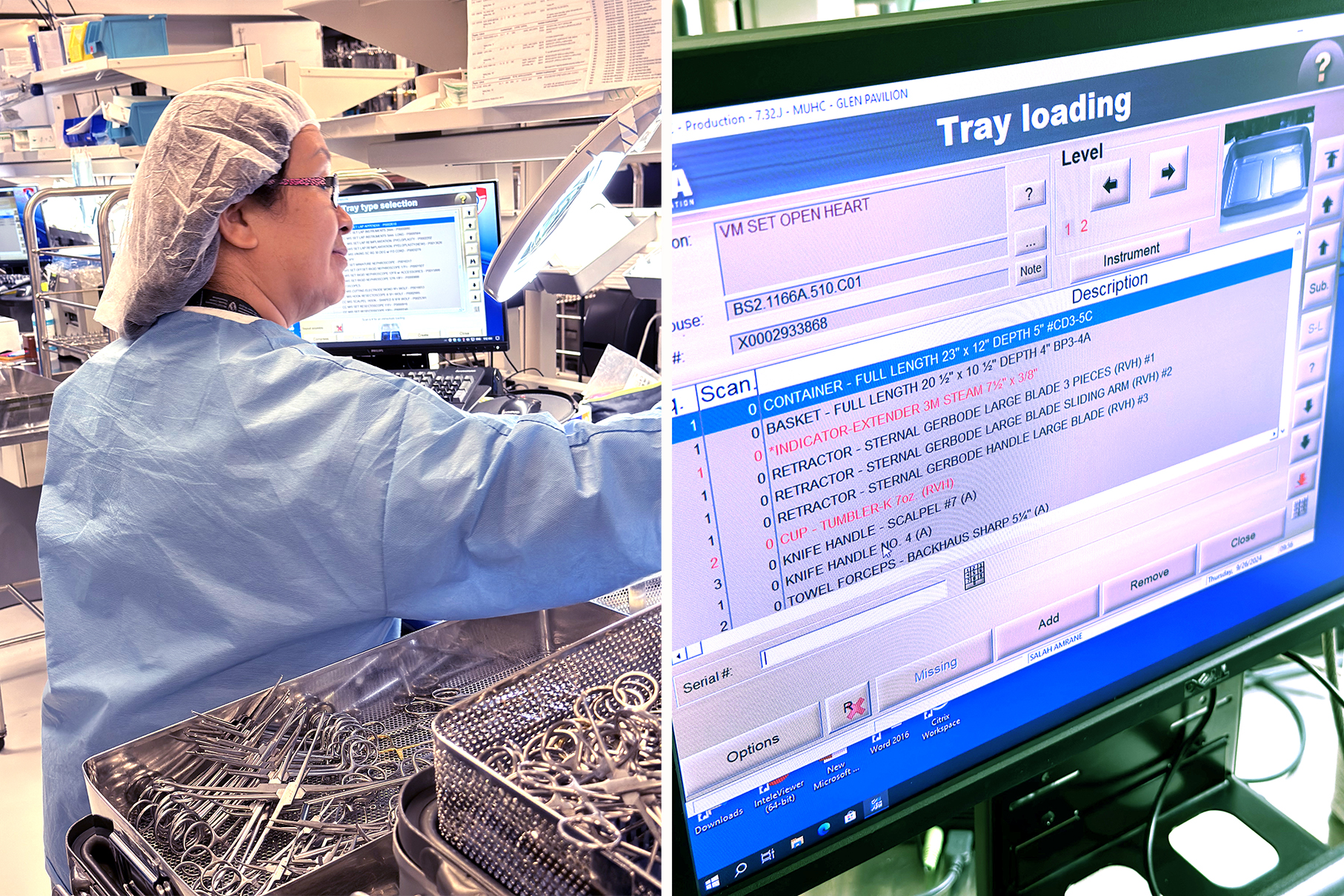
The medical devices then move on to the sterilization stage. This can be done in gigantic autoclaves (steam sterilizers) that raise the temperature to 135 degrees. Each cart is equipped with an internal and external chemical indicator, plus a biological indicator. The external chemical indicator, which enters in one colour on one side, must come out in another colour, confirming the package is sterile. The biological indicator is then incubated to ensure the spores are destroyed, confirming sterilization. Sterilization can also be done using the Sterrad, a unit that enables medical devices to be heated to a low temperature using a chemical process based on hydrogen peroxide.
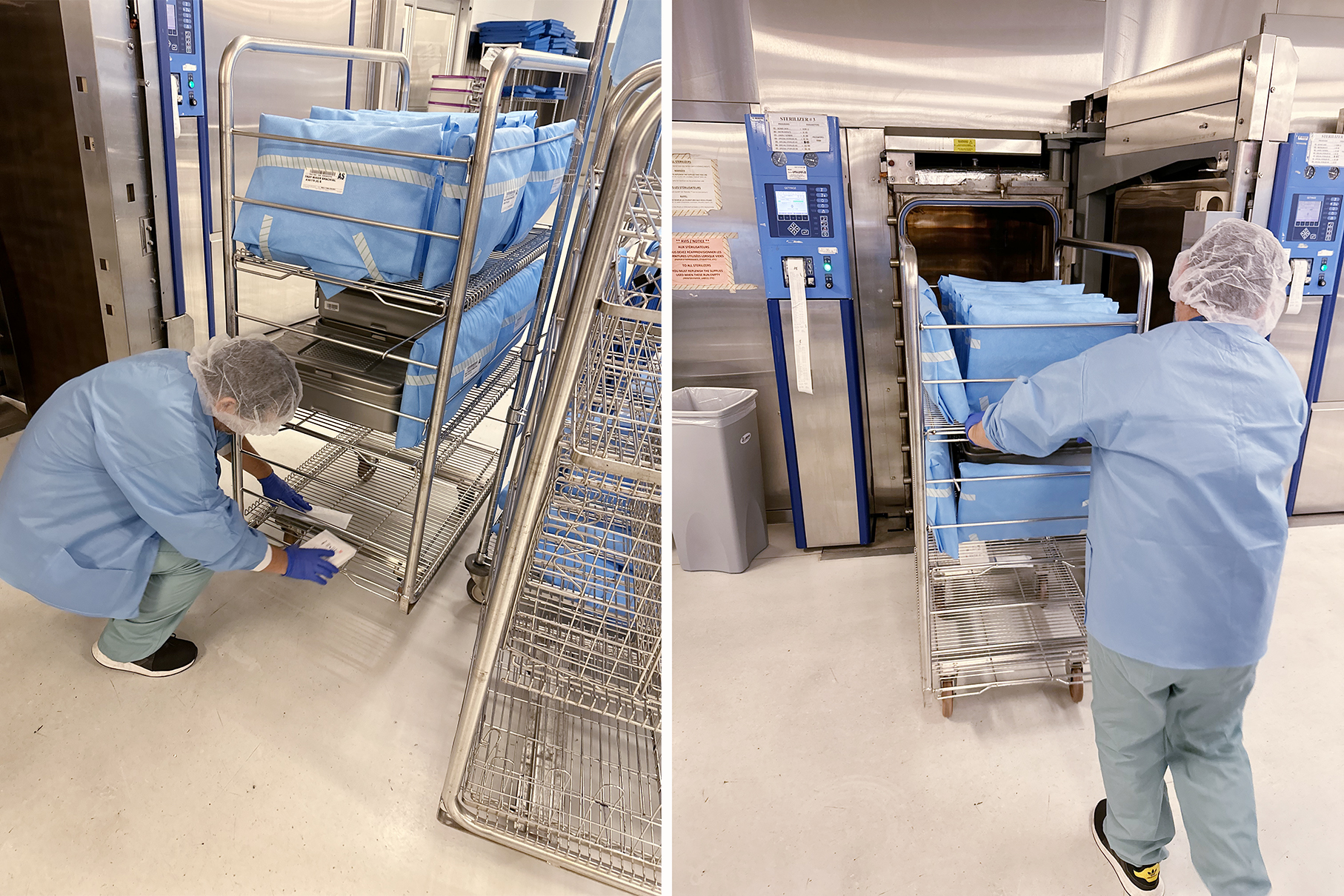
The MDRU also includes several satellite units for flexible endoscopic devices. The reprocessing procedure is known as high-level disinfection, a liquid process for devices that cannot tolerate sterilization. These satellite units serve endoscopy, urology, ENT, and pediatrics.
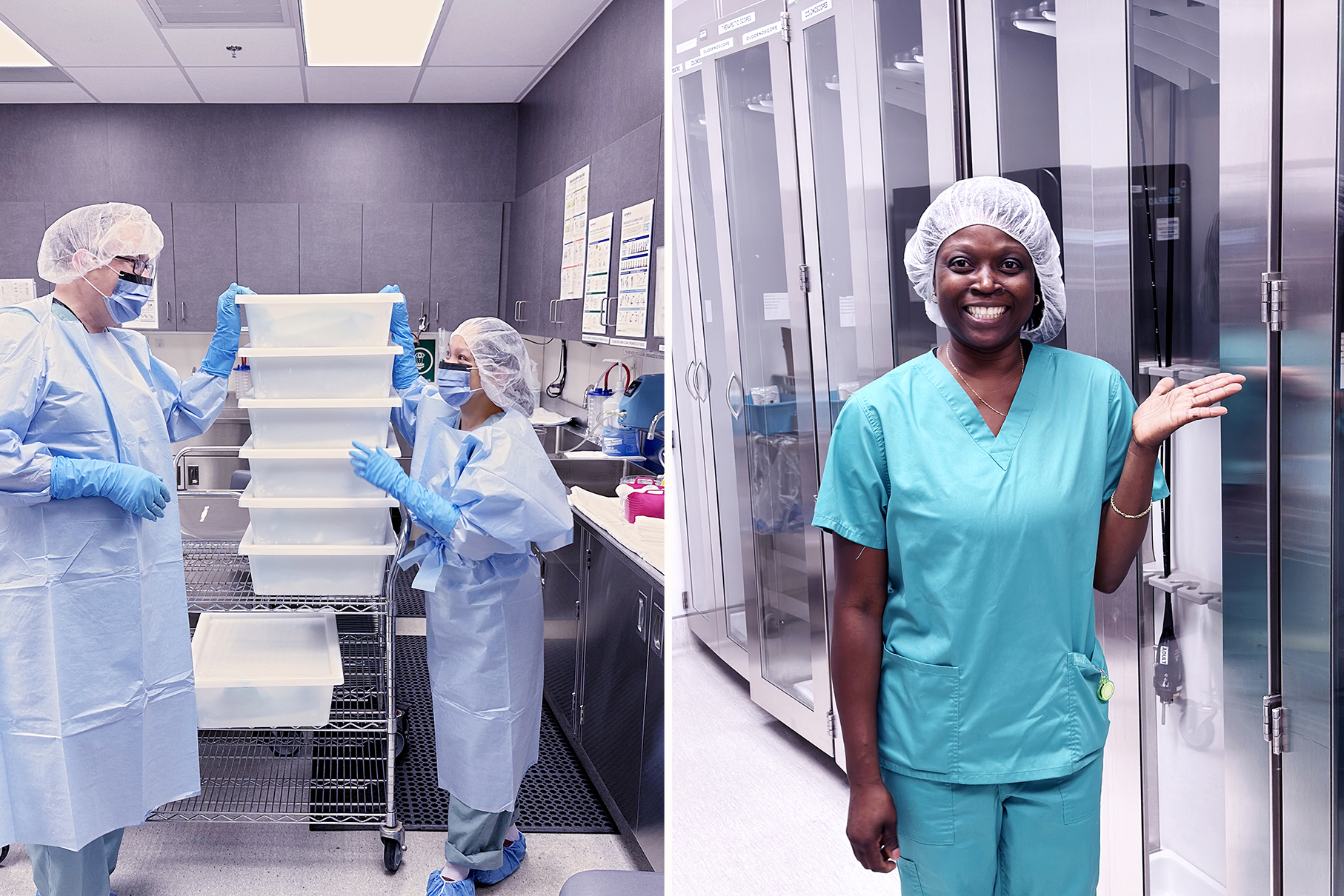
An enthusiastic team
“We do meticulous work that has to be carried out to perfection. At the end of the day, we have a sense of accomplishment,” confides Salah Amrane.
‘When a patient who has undergone surgery leaves with a smile on their face, we know that we have also made a contribution’, addscolleague Carizza Dadayo. “We may not be seen…but we're indispensable!” concludes Xiaoxian Yang.
As part of Medical Device Reprocessing Staff Week, we say: thank you for being on duty day after day to provide exceptional service to patients, young and old!
Did you know?
- The department is always looking for candidates to fill its positions.
- There is a new specialized training program, a DEP (Diploma of Vocational Studies) that leads to the profession.
- The MUHC, in collaboration with the Quebec government, is offering eight scholarships of $10,000 to encourage those interested in DEP training to join the ranks of MDRU professionals.